Features Description
|
Multiple-slide Die Casting Machine
- About Multiple-Slide Die Casting Technology
A “conventional” hot chamber die casting machine generally has two platens – one moving and one fixed. One-half of the die is fixed to each platen. By using various mechanical devices, such as cams, built into the die, complex components can be cast. However, repeatability (part-to-part consistency) tends to suffer over time, due to wear of moving parts, and the tooling is expensive. Injection takes place through the fixed platen, and the cavity is fed through a sprue and runner system, which is filled with liquid metal each time at shot is made. The metal in the sprue and runner system represents scrap material, which usually has to be trimmed off the die cast parts in a secondary operation. It is common practice to add overflows and to vent the tool, in order avoid entrapping the air from the sprue in the casting during injection. The overflows further increase scrap, and venting often results in flash around the cavity.
A “multiple-slide” hot chamber die casting machine has two or more independently movable slides. Each slide carries a die block and operates within a precision slide guiding system (also known as a crosshead). Up to four slides is common, and as six slides are possible. Each die blocks has one or more cavities and/or cores on its face, which together form the complete cavity and runner profile (into which the molten metal is injected). The mating faces of the die blocks are held together by a clamping system, and injection of the molten metal is made perpendicular to the mating faces of the die block (“parting line injection”). Because injection takes place directly on the parting line, there is no sprue. Thus, scrap is reduced, and the cycle time is often much faster, because it is not necessary to wait for the sprue to solidify before opening the die. Also, the various mechanical devices necessary to cast complex parts in a conventional die casting machine can be eliminated by using the additional slides of a multiple-slide machine. Part-to-part consistency is improved and tool cost is reduced. The absence of a sprue significantly reduces the need for overflows (often, they are not necessary), thereby saving material, and the requirement for venting is minimal.
- Multiple-Slide Die Casting Process
Multi-slide tooling is designed to use 4 perpendicular slides in the tool to enable very complex and accurate castings to be produced. In some cases, up to 6 slides can be used, which may be at angles other than 90 degrees. The process is used principally for small zinc components.
The multi-slide tool is made up of the die block, sliders, crosshead and cover plate. Each die block has either a cavity and/or cores on its face, which together form the complete cavity and runner profile into which the molten metal is injected. These die block are mounted onto sliders, which fit precisely into a crosshead, ensuring repeatable opening and closing operations. A cover plate, bolted onto the top of the tool, holds all these components together.
Each slide is managed by a controller, and moves independently of the other, both during the closing and opening sequences. This provides tremendous flexibility, which ensures part integrity and prevents damage to the tool.
Ejection of the parts is achieved with an air-blast, which blows the shot clear of the cavity and into a padded collection mechanism.
- MS Series Multiple-Slide Die Casting Machines
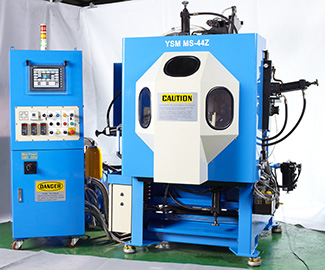 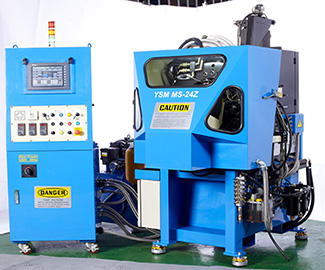
Advantage
It is well known that the characteristics of multiple-slide die casting technology with parting-line injection when applied to the production of small components include:
- High precision;
- Net shape parts, having complex geometry, can be cast;
- Consistent part quality;
- Quick die changeovers;
- In-die de-gating and automatic separation of parts from runners is possible in many cases;
- Flash-free castings;
- Rapid cycle speeds;
- Low tooling costs;
- Elimination / reduction of secondary operations;
- Saving in material, energy & labor.
The result is low cost-per-part, as evidenced by the popularity of multiple-slide technology for small components.
Introduction
Many years ago, it was widely believed that multiple-slide machines were not suitable for the production of components requiring a plating quality finish or could at best produce plating quality on relatively small-sized parts. Unless the part is very small, the small die casting machines do not generally have the injection power required for very high quality surface finish. Indeed, a number of the leading practitioners of the art of multiple-slide die-casting use multiple-slide machines for small components and those require a functional finish, while employing conventional machines for larger components and those requiring a plating quality finish.
In view of this, YeouSheng in the past few years, much research has been undertaken, to improve the machine injection power, clamping ability, multiple-slide process function and multiple-slide tool design technology, to meet the production high quality plating surface finish casting needs, results are summarized as below.
Clamping Systems
For many years, “C-type” clamping systems have been widely used multiple-slide die casting machines with relatively low clamping forces. Such systems are actuated by small pneumatic or hydraulic cylinders, are relatively inexpensive, operate rapidly, and generally perform well in light-duty applications. However, keeping a C-type clamping system closed when die casting larger components, at the injection pressures and velocities necessary to achieve high surface finish, is a challenge. Today, C-type clamping systems have largely been superseded by Ring-type for heavy-duty applications. Below figure Shows the Ring-type clamping system and the slide guiding system of YeouSheng MS series machines, which was purpose-designed for high surface finish applications.
Referring to the four toggle machine, the toggle mechanisms are supported by the toggle pins anchored into massive toggle brackets, which are bolted to the machine table (platen). On the opposite side from the table, a heavy ring is bolted on top of the toggle brackets. The resulting assembly is extremely rigid – the problems of bending of the table (platen) and elastic deformation of the toggle brackets that are characteristic of C-type clamping systems are essentially eliminated by the Ring-type system. Indeed, deflection under load of Ring-type systems has been shown to be less than 10 percent of C-type clamping systems at comparable tonnage.
An automatic lubrication system supplies all elements of the crosshead and toggle mechanisms, thereby minimizing the need for operator intervention, and reducing maintenance costs. Compression regulator within the toggle brackets facilitate rapid, accurate and independent adjustment of the clamping force generated by each toggle system.
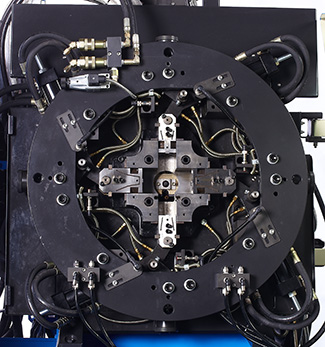 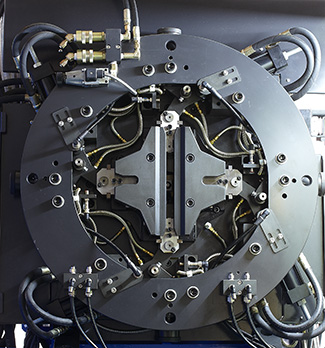
Slide Guiding System
The slide guiding system (crosshead) is completely independent from the clamping system, and is equipped with replaceable wear plates. The table (platen) that supports the slide guiding system is water-cooled, as are the slides (shanks). The slides are connected to the clamping system by universal tenon joints, so that assembly and disassembly are facilitate rapid, and no lateral forces are applied to the slides. The ram of each toggle system bears against a stop within its toggle bracket. The system allows maximum pre-load to be applied without any force being brought to bear on the crosshead.
Using such Ring-type clamping systems, extremely high injection velocities and metal pressures can be employed, without “popping open” the dies.
Development of such clamping and slide guiding systems has been one of the keys to achieving high surface finish with multiple-slide machines.
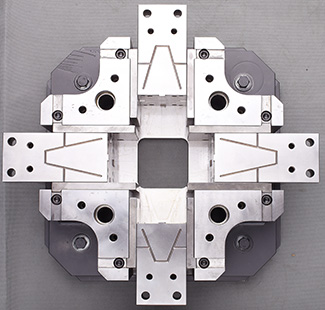
Process Parameters Control System
All the MS series machines are equipped with a programmable logic controller combined with a touch screen operator interface, featuring ease of part programming, machine set-up, program storage and retrieval, integrated access control, and an error messaging system with on-line “help”. The latest generation of control system software is proprietary to YSM; the simple, yet powerful graphical interface is easy enough to be used by just about anyone and reduces the “learning curve” associated with new equipment. An Ethernet module is available as an option, by means of which remote diagnosis of any operational difficulties with the machine can be undertaken.
The YSM has developed process parameters and shot monitoring system (PPMS), which is available as an option. PPMS permit the machine operator to set specific values of up to 12 critical production parameters (e.g. temperatures, injection speed, and fill time). Each process parameter can be programmed with upper and lower limits. In the event that an out of tolerance condition is detected, PPMS can be programmed to do a number of things, such as set off an alarm, stop the machine or direct the components produced to a separate bin, for later inspection. The shot monitoring portion of PPMS is an excellent diagnostic tool for machine operators and process engineers.
A closed loop injection control system is available as an option on MS-44 machines for greater reliability and repeatability. This system permits real-time control of the injection process from start to finish, resulting in stable system performance, premium part quality and significant reduction in the “hammer effect” at the end of the injection, thereby reducing flash. All setting of the closed loop control system for any given mold can be saved on the hard disk of the PC, together with the mold sequence and the PPMS setting, for ease of set-up and repeatability.
The Model MS-24Z is particularly for casting very small, high precision components in multiple-slide dies, at ultra-high speeds.
Injection System
The entire injection system is designed for high performance and repeatability, resulting in maximum process capability. A unique double plunger injection system, which eliminates flow-back of liquid metal in the gooseneck channel between shots, thereby minimizing the volume of air injected into the cavity and reduces porosity.
All MS Series machines are equipped with a precision machined H-13 steel gooseneck, which designed for maximum life and consistent performance.
The gooseneck outlet and nozzle are electrically heated and controlled independently.

Metal Melting System
The metal melting system includes an ingot feeder, a melting pot and a shielding hood. The melting pot is electrically heated for precise control of temperature. The ingot feeder is located above the melting pot, which preheat and feeding the ingot automatically, as well as maintain the melting pot with consistent molten metal level and constant temperature. The melting pot surround shielding hood to ensures person safety and isolated heat source, resulting clean and pleasant working environment.

Hydraulic System
A fully integrated hydraulic system incorporating high flow rate and rapid response valves ensures fast cycle speeds. Clamping is controlled by the function manifold, which also controls the movement of slides and gooseneck. There are six hydraulic functions available to incorporate core pulls and two pneumatic functions to facilitate automation. An independent injection manifold controls the shot speed and pressure, which results in consistent casting quality.
The stand-alone hydraulic power unit designed for easier access to hydraulic pressure adjustment and maintenance to the pump and motor. This unit is equipped with sensors to monitoring oil temperature and level, as well as the condition of filters. These sensors are linked to the control software, which will generate alarm messages, informing the operator of any abnormal conditions.
|